〈工業技術與資訊〉先進半導體薄膜設備智慧製程技術
工業技術與資訊月刊
撰文/陳怡如
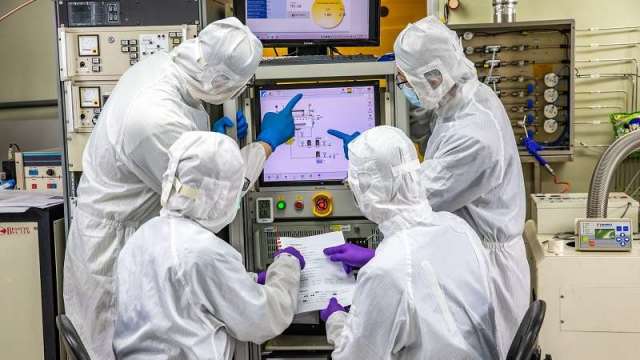
製程參數就像食譜配方,不同參數組合,都會影響良率。半導體電子元件動輒上千道製程中,複雜反應有如黑盒子,只靠人工調整找到最佳參數,曠日廢時。為了解決此問題,研發「先進半導體薄膜設備智慧製程系統」,領先全球首創虛實整合的數位雙生系統,快速找出參數黃金組合,榮獲工研菁英傑出研究獎金牌。
半導體是臺灣在全球高科技版圖的代名詞,而半導體的薄膜製程,可說是晶圓加工的基礎。當一片片晶圓製造完成後,就會進入加工階段,首先會在晶圓表面鍍上薄膜,依據發光、導電或保護等不同需求,這層薄膜可以是氮化鎵、砷化鎵、氮化銦鎵、二氧化矽、氮化矽等化合物材料,後續再接著進行微影和蝕刻製程。
鍍膜少則 2、3 層,多至 10 幾層,就像蓋房子,地基打得好,一層層堆疊上去才能蓋得穩又好。如果薄膜沒有鍍好,就會影響最終晶圓的良率,因此鍍膜製程極為關鍵。工研院機械與機電系統研究所副組長王慶鈞形容,「鍍膜的腔體設備宛如黑盒子,裡面有太多東西在變化,要控制各種化學和物理反應,只有達到非常均勻穩定的狀態,才能鍍出品質良好的薄膜。」
鍍膜時得考慮壓力、流量、溫度等多項參數,組合可達數百種,過去業界都用是靠人的經驗找出最佳組合,非常耗時及耗費成本。王慶鈞解釋,依照製程不同,每次鍍膜時間從幾 10 分鐘,甚至到 8 小時都有可能,以最複雜的 8 小時來說,當這一輪的薄膜品質不如預期時,下一輪修改就要等上 8 小時後才能知道結果,「一天最多只能進行 2 到 3 輪。」
打造真實腔體 突破數據關卡
為了解決這些痛點,工研院獨創製程數位化的預測技術。團隊以理論和真實數據為基礎,建立一套具備多重物理關聯的分析模型 APP,模擬在不同參數下,相對應的薄膜品質,工程師只要輸入不同參數組合,就能預先知道結果,大幅縮短調整和試錯時間,「這對開發新產品特別有幫助,以後就不用再大海撈針尋找參數。」
王慶鈞指出,這和常見的大數據,甚至 AI 人工智慧分析有些不同。大數據分析是建立在大量的數據基礎上,但由於半導體製程往往涉及廠商機密,無法取得太多真實數據,為了突破數據關卡,團隊開發相關技術,只需少量數據即可建立分析模型;更透過虛實整合方式,打造一個接近真實鍍膜設備的腔體,首創「流場可視化」和「電漿診斷技術」,藉此取得更多真實數據回饋修正模型,讓預測更加精準。
所謂的流場可視化,是以雷射光照射腔體,觀察在不同參數下,腔體內的氣體流場變化,王慶鈞比喻,「就像烤麵包機,在烤的過程可以看到蒸氣怎麼跑,好讓麵包烤得均勻。」另一方面,也在腔體內裝設電漿即時診斷模組,收集電子密度、離子能量等電漿參數的變化。
三大效益 鞏固產業競爭優勢
由於薄膜製程牽涉許多複雜因素,這項技術需要物理、化學、材料、電子、電機、機械等跨領域人才參與,「全球很少有這樣跨領域的研發團隊,這正是工研院的優勢」王慶鈞表示。早在研發之初,工研院機械領域與電光領域即攜手合作,由機械領域團隊打造虛實整合平台,半導體經驗豐富電光團隊則扮演驗證角色,修正參數,提升模型準確率,「將模擬和實務操作對接起來,」工研院電子與光電系統研究所研發副組長傅毅耕說。
近年來,團隊不停深入研究各種鍍膜技術,目前已涵蓋市場 9 成以上的鍍膜技術設備,可廣泛應用在半導體先進製程、化合物半導體、5G 無線通訊、Micro LED 與 IC 載板等新興產業的薄膜製程,目前已導入國內外多家半導體元件終端製造商、設備商及系統整合商使用。由於採用 APP 介面,廠商不需大幅改機或替換設備就能使用,降低導入門檻;對設備廠來說,未來若附加參數模擬的 APP 功能,也能進行高值化轉型,同時提高國產半導體設備的競爭力。
有了最佳參數助力,半導體薄膜製程的調機時間,從過去人工調整時的 1 周縮短為 2 小時,新產品開發時間從 3 個月縮短為 1 個月;每一輪製程的重覆性誤差,也從人工調整時大於 4%,降低為小於 2%;預測的準確度更是從過去的人為經驗調控不到 80%,提升至超過 95 % 的高效能。
王慶鈞認為,這項技術還可為產業帶來三大效益。首先是協助臺灣半導體產業數位轉型,從仰賴經驗轉型為仰賴數據的精準預測;第二是加速半導體設備廠技術升級,提供客戶更多附加價值;第三是透過預先模擬,減少製程研發時的材料耗費,並銜接未來半導體製造的數位化整合淨零碳排趨勢。三大效益,三管齊下,持續鞏固臺灣半導體產業的競爭優勢。
轉載自《工業技術與資訊》月刊第 364 期 2022 年 7 月號,未經授權不得轉載。
- 僅此一場!專家教你如何抓住獲利機「匯」
- 掌握全球財經資訊點我下載APP
上一篇
下一篇